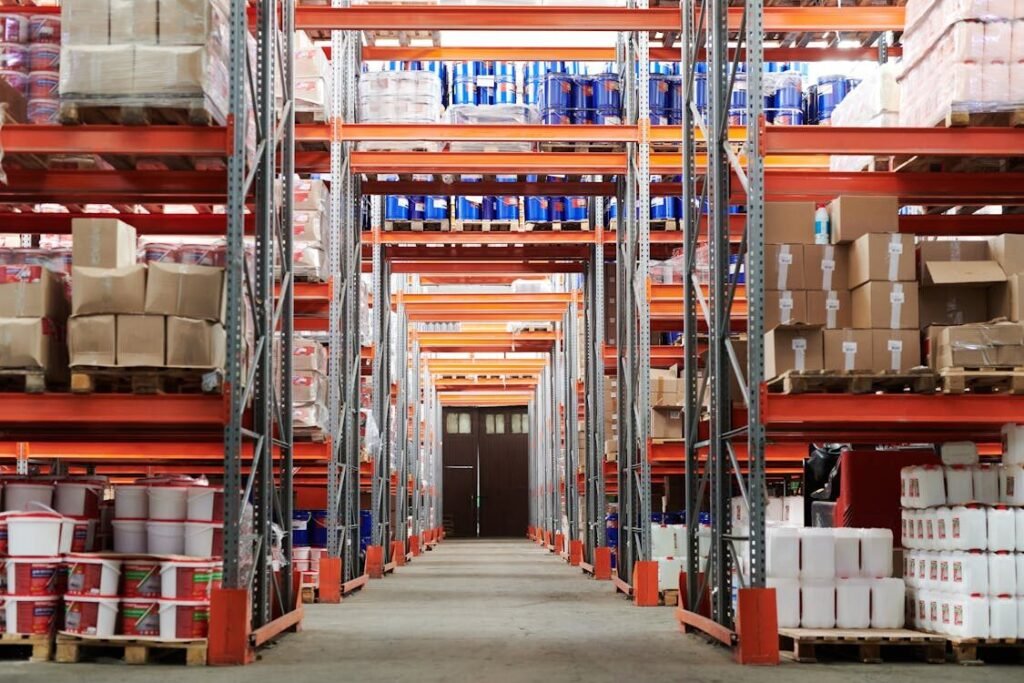
Japan has always amazed the world with its practical approaches. The Kanban System is one such lean manufacturing tool that provides a signal system for workflow and inventory management during a production process.
What is needed, when it is needed, and the right quantities define this approach comprehensively. Kanban focuses on providing timely information in optimizing inventory levels, and managing the workflow while reducing waste,
Eager to learn more about Kanban systems? Stick to us till the end to learn about this amazing Japanese approach in detail.
History of Kanban Systems
The manufacturing world must be indebted to Taiichi Ohno, A Toyota engineer, who developed the Kanban System from 1940 to the 1950s. The story started with a crucial problem: “Overproduction” in Toyota Motor Corporation. Overproduction results from excessive demand for the product, which as a result piles up inventory, takes up space, and seizes capital.
The Toyota Production System, as a part of the Toyota Corporation thus worked out on it, and crafted several tools to drive efficiency and waste reduction, one of them being the Kanban System, which emphasizes increasing efficiency and reducing waste through a simple signaling system.
Kanban System: Peeling the Layers of the Concept
This system is based on the “Just In Time production” concept, which means ordering or producing products only when they are needed in the required quantities. It strongly discourages excessive inventory.
The kanban system greatly relies on visual aids. Using cards or bins, the system communicates to pinpoint the tasks to be performed like inventory in need. To communicate between different parts of the supply chain, these cards or visual aids are used to communicate. These signals communicate inventory levels and re-order/refill requirements.
When inventory reaches a predetermined level, a triggered Kanban signal initiates the re-ordering process calling for more inventory to be ordered or produced.
Kaban & The Visual Inventory Loop
The visual loops in the Kanban system are of great importance.it is through them basically that the whole communication throughout the supply chain takes place.
Kanban Boards | It is a visual board with columns representing the workflow. For instance, it indicates “To Do”, “In progress” or “Done.” |
Kanban Cards | These are dedicated cards for each inventory item. They contain useful information like ideal stock levels, due date, work status, recorder points, etc. |
Work in Progress Limits | Each stage in the manufacturing process is assigned a WIP limit. It indicates the number of items in progress stored in inventory and thus prevents bottlenecks. |
Kanban Loop | The cards circulate in a kanban loop, triggering responses. For instance, when the products are consumed, the card moves to the “Replenishment Needed Center.”. This initiates restocking, after which the card moves to the “To Do” section. |
Types Of Kanban Systems and Inventory Management
Each type of Kanban system is listed below.
Type | Description |
Production Kanban | This is the classic Kanban type, used in manufacturing setups.It involves the management of finished products; from production to customers.It triggers a signal about when to produce more goods |
Withdrawal Kanban | It focuses on managing raw materials needed for productionThese cards are attached to the raw material containers, when one of them is emptied during the production line, the card signals withdrawal of material from storage. |
Supplier kanban | It facilitates & streamlines communication with suppliers.The cards with specific requirements are directly sent to the suppliers, who manage the supply accordingly. |
Emergency Kanban | This acts as a backup plan in emergency situations. These cards are different from other cards and are designed to initiate requests for emergency situations like machine breakdowns etc. |
Express Kanban | These are similar to emergency Kanban but represent situations less intense and critical than the former. |
Implementing Kanban- A Step-by-Step Guide
Define Your Workflow
Before starting, manufacturers need to define their production workflow. Try the following practices.
Identifying stages: It requires you to map out the entire process by breaking it into steps and then identifying each of them. Disintegrate the whole process into steps like “To Order”, “In Storage”, “Picking”, and “Packing”.
Visualizing the Steps: Acquire a Kanban board to translate the flow visually. For this purpose either a digital Kanban software board or a simple whiteboard with columns and sticky notes. Each column represents a stage. The board does not need to be complex or look amazing but must be able to convey the inventory levels and kanban cards in an easy-to-understand way.
Create Kanban Cards
Create a kanban card for each inventory item. Include all the important details such as the name, Recorder point, Ideal Restock level, and potential Supplier information.
Make sure to maintain a format for your cards that makes the identification easy.
Set Work In Progress Limits:
Setting work in progress limit is a core principle that sets limits in each step and prevents bottlenecks with built-up inventory.
The best way to do so is to start with conservative work limits. Later adjust them slowly according to the team’s capacity.
Implement a kanban Loop:
Maintain the kanban loop. Send the car to the “Replenishment needed Section” when the raw material is consumed. Cards are of great importance here as they act as visual triggers, initiating an action according to the situation.
Establish a Communication & Feedback Mechanism
The best way to communicate with team members is to do so in front of the Kanban board. Also, regularly ask for the members’ feedback to improve the workflow and inventory management.
Pros and Cons of Kanban:
Let’s have a look at the pros and cons of Kanban.
Pros of Kanban Systems:
- Improved communication
- Enhanced inventory management
- Minimal wastage
- Flexibility and adaptability
Cons of Kanban Systems:
- It’s complex and requires ongoing maintenance
- The system is a bit costly
- Kanban relies majorly on suppliers.
Lean Philosophy & Kanban System: Discovering the Connection
Lean philosophy and the Kanban system have a lot in common! Let’s learn how.
Lean Manufacturing advocates the philosophy of efficiency that keeps customer service and satisfaction ahead of anything. This system also ensures waste reduction throughout the manufacturing by constantly emphasizing productivity, efficiency, and efficient resource utilization.
And here’s how the Kanban System resonates with the former.
Reducing Waste: Utilizing principles like Work In progress, Kanban ensures nothing goes to waste and controls overproduction.
Just-In-Time: Kanban ensures inventory control. In other words, it triggers a manufacturing or purchase warning only when it’s needed.
Empowering Teams: Kanban keeps everyone in the loop, empowers the team, and ensures that collaboration leads to dedicated teamwork and a smooth running process.
Continuous Improvement: The workforce strives for continuous improvement through visual aids by identifying bottlenecks and monitoring workflow.
Conclusion
Kanban systems are a great way to manage inventory and maximize an efficient workflow. Using cards as visual aids, this system ensures communication through the Kanban cards to manage the inventory by signaling restocking, etc. Based on the JIT principle, this lean manufacturing approach has been adopted worldwide to achieve the desired goals.